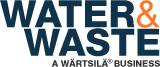
Cruise vessels are responsible for around 25% of all solid waste produced on ships worldwide. Due to various restrictions and regulations, they face the challenge of having a limited operational window for removing waste from ships. Therefore, there is an ever-growing demand for waste management systems with a strong focus on volume reduction and effective storage of waste. Wärtsilä’s systems and product range don’t only meet this need for cruise ships but are also suitable for all vessel types and sizes.
The accumulation of recyclable wastes on board vessels must be managed correctly. Wärtsilä’s systems provide specific volume reduction through a range of processes, resulting in decreased handling time, maximised storage space as well as augmenting efficiency of offloading.
Wärtsilä is able to work with the shipyards and owners to optimize the use of the available space on board through careful design and equipment specification and improving workflow.
Cruise vessels represent 4% of the world’s shipping tonnage producing 25% of the world’s dry waste
SHREDDER
BALE COMPACTOR
DENSIFIER
GLASS CRUSHER
BRIQUETTING MACHINE
SHREDDER
The largest volumes of waste produced by a vessel are due to packaging. Clean and contaminated cardboard, plastics and packing materials take up a significant volume on the vessel.
The shredder takes raw waste material and cuts it down to much smaller pieces allowing a press to further reduce the volume of the material or a high surface area for burning in the incinerator.
Shredded waste may be baled, compacted or pass to the dry waste silo for feeding into the incinerator.
BALE COMPACTOR
Waste cardboard from packing of food and dry products makes up a significant volume of the ships daily waste material.
The bale compactor crushes this material into bales which are clamped and palleted for easy storage. This recyclable material can then be passed to shore providing the most environmentally sustainable pathway for this waste stream.
Compaction provides the most effective volume reduction for this waste stream. Bales from clean material are stored on the vessel and then passed to shore for recycling. Bales from contaminated cardboard are stored in a cold room and passed to shore for processing.
DENSIFIER
Food tins and drinks cans are a high volume waste all of which is considered contaminated. Very often this waste can become odorous and a hazard to health in storage. This material is recyclable and is passed to shore for this purpose.
The tin densifier applies intense pressure to the waste metal material crushing it into bales a fraction of the volume of the original waste.
The crushed bales are stored in a cold storage area and passed to shore for recycling.
GLASS CRUSHER
Glass from drink bottles and food storage are a high volume contaminated waste stream. Very often this waste can become odorous and a hazard to health in storage. This material is recyclable and is passed to shore for this purpose.
The glass crusher passes this material through shredder blades which reduce the glass to very small particles. This significantly reduces the volume of the material producing a waste that is more manageable to store.
The crushed glass is stored in a cold storage area and passed to shore for recycling.
BRIQUETTING MACHINE
Mixed waste streams on cruise vessels provide a significant challenge to the operator in both in terms of storage and discharge to shore and in terms of transport.
The briquetting machine takes mixed or single source wastes, shreds them, then turns them into waste brick by applying significant pressure. The resulting waste stream has a very much smaller volume allowing efficient storage or a manageable waste for gasification.
Briquettes from clean material are stored on the vessel and then passed to shore for recycling. Those from contaminated cardboard are stored in a cold room and passed to shore for processing. Both waste stream are suitable for feeding to the Wärtsilä gasification unit where they are reduced to char and bagged.
A key challenge for cruise vessels is the management of large volumes of waste both within the vessel during transit and in passing the waste to shore in a limited time window. As part of an over all service package Wärtsilä Water & Waste specialists can work with the shipyards and owners to look at workflow and offloading strategies to minimize the impact of this storage space and to expedite the transit of waste to shore.
All lifting and transport devices for both compacted waste and ash bags can be supplied by Wärtsilä Water & Waste as part of an overall supply package giving a “one stop shop” for all supply and support needs whenever and wherever you require it.
Servicing and after-care is available for new builds and retrofits. For more information on this, please complete the ‘Contact Us’ form on the webpage.
Our customers are facing a jungle of environmental regulations. Wärtsilä Water & Waste guides the customers through the whole process of being compliant, from feasibility studies to installations and maintaining the equipment, and offers the opportunity to become environmentally sound in the easiest way possible.
Compliance, energy efficiency, and environmental awareness among companies’ customers and stakeholders all play a major role in decision-making. Environmental planning helps companies to reduce emissions and consider regulations while improving operational efficiency and building a green reputation.
The solution for our customers is more optimised performance, as it reduces downtime, fuel consumption and costs – meaning less pollution and ultimately a positive financial impact.
New demand from cruise yards for integrated waste treatment systems
Compliance with environmental regulations requiring effluent from cruise ships to be clean and safe
Risk of penalties if discharging waste overboard
Complete wet and dry waste treatment package that meets and exceeds the likely regulatory requirements for both new and existing installations
Wärtsilä’s treatment systems offer a cost-effective and safe means to avoid discharging waste to the sea
With total waste management the efficient process of collection, recycling and disposal provides high efficiency with the lowest impact on the environment.
Please fill in the form, we aim to respond within 1-2 business days depending on the enquiry. For an existing installation, provide all necessary details to identify the installation and the equipment. Fields indicated with an asterisk (*) are required.
For NEWBUILD & RETROFITS, please contact +44 1202 662 600 or waw.sales@wartsila.com
For spare parts, please e-mail us with the Equipment Serial Number or the name of the vessel at pse@wartsila.com. For urgent support, contact +44 1202 662 634.
For technical support & service, please email us with the Equipment Serial Number or the name of the vessel at poole.service@wartsila.com. For urgent support, contact +44 1202 662 616.
Equipment Serial Number is taken from the equipment nameplate and includes all letters and numbers as given on the equipment nameplate.