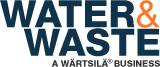
A crucial first step in UV and EC ballast water treatment is the filtration of all incoming seawater during uptake. We use high quality 40 micron back-flushing filter systems that offer an exceptional high and reliable performance. They allow for a very consistent second stage treatment of the ballast water to IMO and USCG standards. Our filter systems are designed by our trusted partner FilterSafe®.
The patented nozzleX technology cleans 100% of the filter screen every time, without any wear on the nozzle or the screen
Water starts its journey to the ballast tank by being pumped onboard. It may go immediately to the filter or have to travel a distance across the ship to get there. Once it arrives at the filter, it goes through a prefiltration section that removes large particles. The smaller particles then enter the filtration chamber where organisms and dirt are trapped by the screen. As more and more particles build up on the screen, a sensor recognizes a difference in the pressure of the water coming into the filter and going out of it. This triggers the automatic self-cleaning cycle, where the dirt on the screen is sucked up by the nozzles and is dumped overboard. The pressure returns to normal and the filtration continues. At this point the water is ready to go to the secondary treatment stage to be neutralized before filling the ballast tanks.
Please fill in the form, we aim to respond within 1-2 business days depending on the enquiry. For an existing installation, provide all necessary details to identify the installation and the equipment. Fields indicated with an asterisk (*) are required.
For NEWBUILD & RETROFITS, please contact +44 1202 662 600 or ballastsales@wartsila.com.
For SPARE PARTS, please e-mail us with the Equipment Serial Number or the name of the vessel at pse@wartsila.com. For urgent support, contact +44 1202 662 600.
For TECHNICAL SUPPORT & SERVICE, please email us with the Equipment Serial Number or the name of the vessel at poole.service@wartsila.com. For urgent support, contact +44 1202 662 600.
Equipment Serial Number is taken from the equipment nameplate and includes all letters and numbers as given on the equipment nameplate.