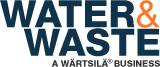
Wärtsilä's Aquarius EC Ballast Water Management System (BWMS) provides a robust solution for the treatment of ballast water using a simple two stage process comprising of filtration and electro chlorination (EC) dosing, across the full range of ship operating and environmental conditions. The TRC is up to 4000 m3/h for a single system.
The system is easy to integrate, operate and maintain while being type approved to the latest IMO and USCG regulations. It is available in for installation in both engine room and hazardous areas on tankers as an EX version.
Wärtsilä Water & Waste works in close cooperation with its customers. Our BWMS partnership program covers all stages, from fleet evaluation to lifecycle support. Wärtsilä’s tailored solutions help minimize your environmental footprint, improve operational efficiency and comply to IMO and USCG standards.
KEY BENEFITS
MODELS
TYPE APPROVALS
SCOPE OF SUPPLY
KEY BENEFITS
MODELS
System | Capacity (m3/h) | Total Installed power (kW) Installed / Nominal |
---|---|---|
AQ-550-EC | 55 - 550 | 38 / 33 |
AQ-1200-EC | 120 - 1200 | 75 / 65 |
AQ-1650-EC | 165 - 1650 | 104 / 90 |
AQ-2500-EC | 250 - 2500 | 161 / 140 |
AQ-3300-EC | 330 - 3300 | 202 / 174 |
AQ-4000-EC | 400 - 4000 | 245 /211 |
Pressure drop
Normal operation: 0.3 barg
Backwash set point: 0.8 barg
TYPE APPROVALS
SCOPE OF SUPPLY
Delivered as standard
Options
Our electro chlorination system works intelligently. It always provides the dose needed to meet the type-approved parameters for treatment of the ballast water
The operation of the EC system is incredibly straight forward. Simply selecting an operation mode and starting the ballast pump when requested. Dosing and adjustment are fully automatic during operation process.
Crew interaction is mainly limited to only maintenance needs (TRO reagent change, bisulphite stocking) and occasional watchkeeping of the unit.
The Aquarius EC uses an in-situ electro chlorination system to provide the second stage of treatment during ballast uptake. The system works intelligently to always provide the dose needed to meet the type approved parameters for treatment of the ballast water. Dose control is a critical part of the treatment process and essential to treatment success.
On discharge, the water is neutralised, only if needed. A small dosing set is used to administer Sodium Bisulphite. This is required to meet both IMO and USCG chlorine discharge standards. The system is safe, highly effective, sustainable and extremely scalable.
A crucial first step in EC ballast water treatment is the filtration of all incoming seawater during uptake. We use high quality 40 micron back-flushing filter systems that offer an exceptional high and reliable performance. They allow for a very consistent second stage treatment of the ballast water to IMO and USCG standards. Our filter systems are designed by our trusted partner Filtersafe®.
Water enters the vessel through the seachest and is pumped by the ballast pump to the first stage of the treatment system, the filter. At the filter, the water is first prefiltered to remove large particles and debris. The particles less than 1mm then enter the filtration chamber where they pass from the inside of the screen out to the filter body.
After filtration, the seawater is ready to go to the secondary stage to be disinfected before filling the ballast tanks.
As the water passes through the filter, organisms and dirt are trapped on the inside of the screen. A differential pressure sensor measures the amount of debris trapped on the screen and triggers the automatic self-cleaning cycle when the screen needs cleaning. During the self-cleaning cycle, the organisms and dirt on the screen are suctioned by the nozzles back through the scanner arm and deposited by the flushing system overboard.
After cleaning, the differential pressure returns to normal and the automatic cleaning cycle resets until the next time the screen needs to be cleaned.
Please fill in the form, we aim to respond within 1-2 business days depending on the enquiry. For an existing installation, provide all necessary details to identify the installation and the equipment. Fields indicated with an asterisk (*) are required.
For NEWBUILD & RETROFITS, please contact +44 1202 662 600 or ballastsales@wartsila.com.
For SPARE PARTS, please e-mail us with the Equipment Serial Number or the name of the vessel at pse@wartsila.com. For urgent support, contact +44 1202 662 600.
For TECHNICAL SUPPORT & SERVICE, please email us with the Equipment Serial Number or the name of the vessel at poole.service@wartsila.com. For urgent support, contact +44 1202 662 600.
Equipment Serial Number is taken from the equipment nameplate and includes all letters and numbers as given on the equipment nameplate.